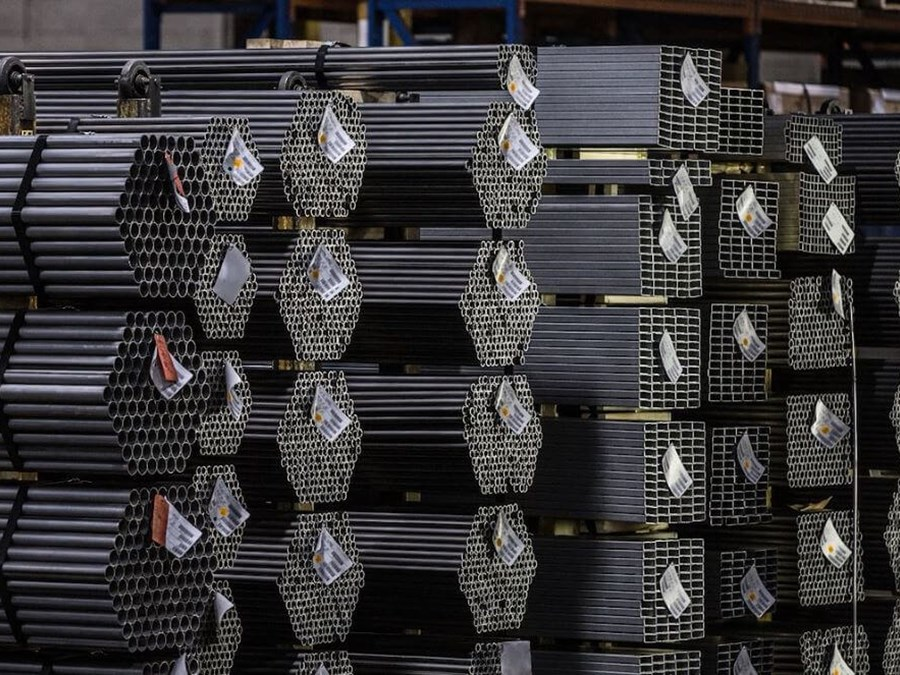
Industry:
Steel Products
The Client:
ArcellorMittal is the world's largest steel maker and is involved in the processing, finishing and distribution of steel.
ArcelorMittal Woodstock Reducing the Environmental Impact of its Operations
ArcelorMittal implemented the Sustainable Energy Plan Training to identify no-cost energy savings and optimize utility management. By engaging various departments, the plant achieved significant reductions in energy use across the organization.
The Challenges
- Identifying and eliminating redundant energy loads.
- Maintaining consistent monitoring and reporting of energy use.
- Aligning plant operations with fluctuating energy markets.
- Securing buy-in from multiple departments and employees.
- Navigating utility rate and regulatory changes.
The 360 Solution
- Training & Awareness: Conducted Sustainable Energy Plan Training to identify no-cost energy-saving opportunities.
- Cross-Department Collaboration: Engaged automotive, tube, and maintenance divisions to target energy inefficiencies.
- Monitoring Systems: Used the Energy Coach Program’s online reporting system for real-time data monitoring.
- Procurement Best Practices: Optimized supplier contracts and utility account management to reduce costs.
- Utility Engagement: Partnered with local utilities to leverage incentives and ensure regulatory compliance.
- Employee Communication: Maintained frequent updates via company boards to build awareness and participation.
The Results
- Reduced weekend energy loads by 500 kW through targeted shutdowns.
- Turned off 83 redundant items, lowering baseload to 20% of plant operating level.
- Achieved $37,000 in additional savings from procurement strategies.
- Initiated energy-efficient lighting upgrades using saved funds.
- Strengthened alignment with utility incentive programs and regulatory changes.
- Fostered a culture of energy awareness and efficiency among employees.
In 2008, Arcelor Mittal Woodstock embarked on their journey towards a more sustainable energy culture. The plant enrolled in the Energy Coach Program offered by 360 Energy with utility sponsorship from Union Gas and generated annual savings over $400k. The site had recently undergone a dramatic change in consumption pattern/level due to fluctuating production mixes and the launch of a new internal production program.
As a result, energy management was at a stand still with no coordinated approach to reducing energy consumption. The baseload for the plant was approximately 30% of its full operating load. The reduced activity shifts such as midnights were also near 50% of full operating load. Due to the complexity of the plant and the size of operations, the team began looking for simple solutions to reduce the energy usage during idle/low production periods.
To get started, the team underwent the Sustainable Energy Plan Training. Here, they began pulling together the basics of when, where, and how to look for these no-cost savings. With the aid of the various departments on the plant floor, the program slowly began taking shape. The targets were set out with annual savings values calculated for each level of reduction. Each weekend, the plant would identify and target more redundant loads and check on previous items that were to be shut down. The plant identified and turned down 500 kW for the weekend period. This was due to a large campaign throughout the automotive, tube, and maintenance divisions of the plant. All plant-level efforts were led by team lead, Ed Pace. Each day, the online reporting system provided through the Energy Coach Program was monitored for excessive variations.
The site was able to identify and turn down 83 redundant items in the plant. This has reduced the baseload to 20% of the operating level of the plant. Using funds from the savings, they are now investigating lighting solutions to create more light with less energy.
However, it doesn't stop there. A progressive organization like ArcelorMittal also continues to drive savings through the financial arena as well. With the gas and oil market crash, the plant was looking very closely at their annual budget. After reviewing options and bids from tier 1 suppliers, the plant was able to save an additional $37k through best practices on procurement and utility account management. The strategy reduced their budget for the winter gas period and solidified their input costs.
The local gas and electric utility were also involved and updated as to the progress of the plant to determine the impact of rate changes, regulatory rule changes, and new incentive programs available to the site. The employees were continuously updated on the progress with frequent energy postings on company information boards.