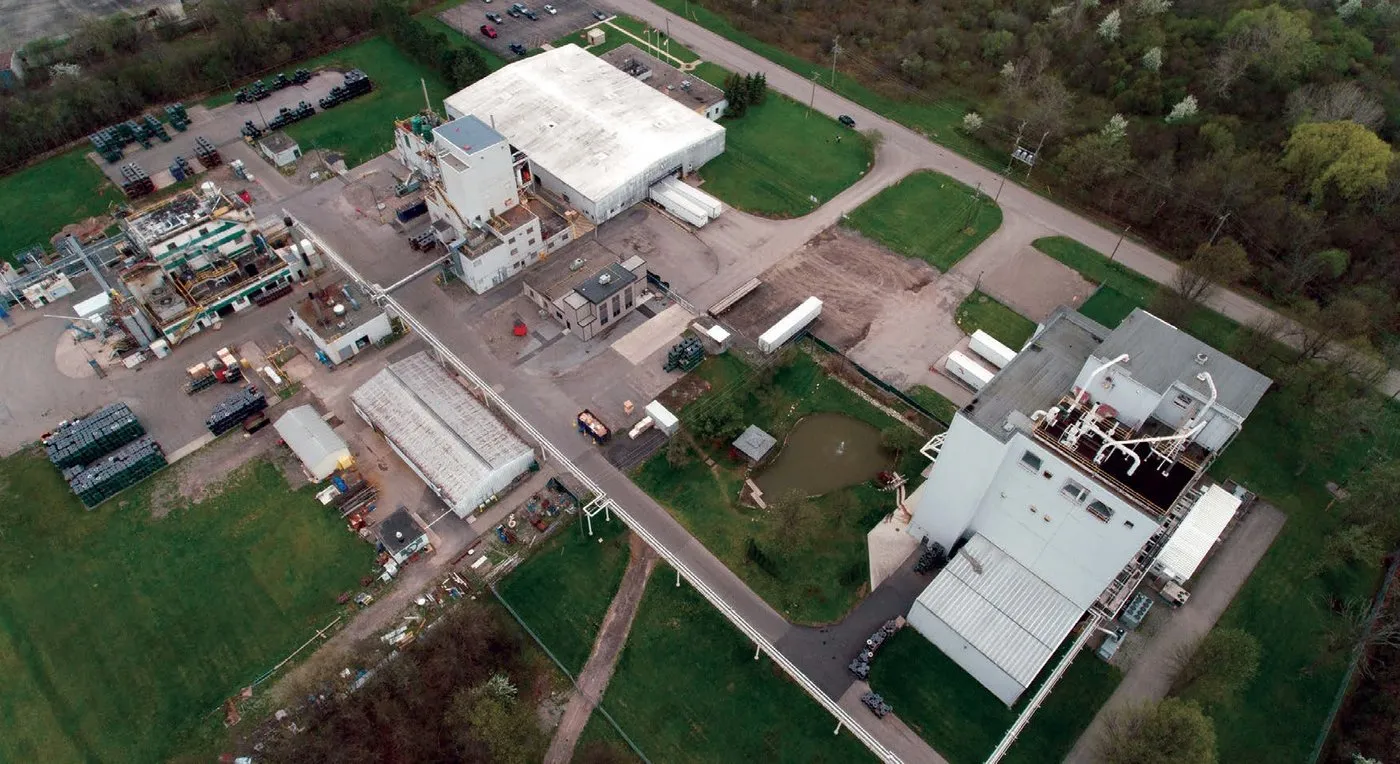
Industry:
Manufacturing
The Client:
Durez Canada is part of Sumitomo Bakelite, located in Fort Erie, Ontario. The site produces high-performance plastic composites for various industries
World-class Energy Management Gives Durez Competitive Advantage
Durez Canada invests in energy management with 360 Energy to enhance efficiency, save costs, and foster a culture of continuous improvement.
The Challenges
A manufacturer of high-performance plastic composites in Fort Erie, Ontario, Durez faced intense global market competition that necessitated better energy management. Their production process involved complex energy requirements across multiple sources – electricity, air, and steam – making efficient management challenging. They needed to modernize their approach to energy budgeting and create a more energy-aware workforce to remain competitive.
The 360 Solution
- Energy Audits: Conducted air and steam leak audits, and installation audits.
- Energy Management Information Systems (EMIS): Implementation for better energy tracking.
- Strategic Energy Planning: Annual plans and training in energy best practices.
- Regression Analysis: Provided predictive cost models for energy usage.
The Results
- Cost Savings: Saved $180,000 through air and steam leak audits and an additional $80,000 through EMIS implementation.
- Energy Savings: Reduced energy consumption by 492,000 kilowatt-hours.
- Cultural Shift: Established a culture of continuous improvement in energy management.
Energy management is an important tool for managing competitive risk, says Rob Hunt, Plant Manager for Durez Canada. “When I read the predictions for future energy prices, I knew we had to address energy input costs now, not wait for them to hit us”, he said. That insight motivated Durez to take action on better managing energy in their company. In 2014, they formally enrolled in 360 Energy’s Journey to Energy Excellence program.
Hunt credits Dave Arkell, CEO of 360 Energy, with encouraging Durez in their new approach to energy management.
“Dave [Arkell] had been talking to us for 3 or 4 years about developing a formal program. We’ve always been cost conscious. But we finally decided to be more proactive and enrolled in the Journey to Energy Excellence program,” Mr. Hunt said. “We’ve just recently started down this path. But already we know we have a firmer grip on how much energy is costing us”, he added.
Durez Canada manufactures phenolic resins and molding compounds widely used in the automotive parts industry. It has had a presence in Canada since 1970 and has been part of global focused Sumitomo Bakelite High Performance Plastic Division of the Sumitomo Bakelite Group out of Japan since November 2000.
Durez has assembled a cross-functional “Energy Task Force” from different functional areas of the plant. The team consists of engineering, finance, and maintenance personnel.
“It takes more than one person”, Hunt observed. “We need mechanisms that help us provide immediate feedback on the consequences of our energy use. The team approach will help us build those mechanisms”, he said.
Even though they have only recently begun the 360 Energy program, Durez has already seen benefits. Company managers have been learning the many ways in which energy is used in the company. “It has helped us start getting out the energy message more broadly throughout the company”, Rob Hunt observed.
His comments were echoed by Mandy Wychreschuk, Engineering Manager at Durez. “So far, the big advantage of the Journey to Energy Excellence has been helping us learn. We have a more in depth understanding of the natural gas market. As another example, it has helped operations decode the procurement process”, she said.
The Journey to Energy Excellence program will eventually change the culture at Durez, according to Rob Hunt. “The changes we need won’t happen overnight. I see the value of this program in changing the way we see ourselves. Eventually, we need to become an energy efficient plant that manufactures, instead of a manufacturing plant that uses energy. That is how we will remain competitive into the future”, he said.
”Prior to the program, we used to base our budgets on trends history. Now what I have, that's different from before, is I can predict my cost. We actually have regression analysis equations that my engineers gave me for both plants, so now I can actually predict what my energy will be.“